This article by Eli Plaskett originally appeared in Modern Machine Shop magazine.
Why do some attempts to implement Industry 4.0 solutions fail?
According to Dr. Stephan Biller, vice president of product management at IBM Watson and a veteran of both General Electric and General Motors, digital solutions fail when people lose sight of their purpose: “If you do not make the lives of the people on the floor better,” he says, “you are guaranteed to fail.” This philosophy has spurred the development of an asset-management and machine-monitoring tool that enables shops to reduce equipment downtime by focusing on both the machinery and those who operate it.
Artificial Intelligence as a Maintenance Tool
According to Dr. Biller, Maximo differentiates itself from other Internet of Things (IoT) offerings by using what he calls true artificial intelligence (AI). “True AI does not simply follow an algorithm,” he says. “True AI learns.” This means that Maximo does not simply react to if/then commands in its code. Instead, it analyzes data input from machinery and predicts when breakdowns are likely to occur.
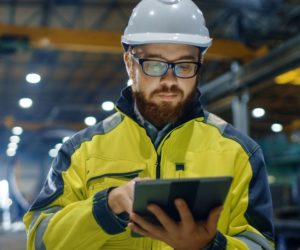
At first, a shop using Maximo to monitor its machines will receive alerts when they are not performing to the necessary specs. Once a machine is fixed and the repairs are logged into the system, Maximo will keep track of the data that the machine was providing in the days leading up to the problem. Further, it will track what repairs were made and how the machine functioned afterward, gaging whether or not the repairs were effective.
The next time the machine approaches a state like the one it demonstrated before breaking down, the system flags it for preventive maintenance and suggests which machine components need attention. Over time, Maximo can recognize different failure states and their root causes. It can then schedule a maintenance request, order parts when needed and calculate their delivery time to coincide with the request. When maintenance staff make repairs and log them into the system, it will accept their input on whether a given process works for a given maintenance issue or machine failure.
“If you do not make the lives of the people on the floor better, you are guaranteed to fail.”
Additionally, the system can understand machine manuals and give suggestions to maintenance staff based on that information. If the suggestion is not helpful, the person can let the system know that its suggestion did not work, and it will accept that information and provide different suggestions. According to Dr. Biller, “The more the team interacts with and uses Maximo, the better it will be at keeping machinery in working order.” That’s the value of true – or learning – AI in a machine-monitoring system.
Managing Assets, Not Managing Machinery
While Maximo can serve as a machine-monitoring system, it is not limited to only that. Yes, it monitors machines, but it also provides direct assistance in assigning personnel and carrying out tasks. It does this through scheduling not only what maintenance needs performing and when, but by scheduling who carries out those repairs.
The system also monitors the progress of the employees at the shop. It identifies technicians by experience and expertise, and it can recommend the right technician for the right job. On top of that, the system can identify employees who are in need of experience and assign them to tasks that will provide them with meaningful learning opportunities.
“The technician of the future will use automation to improve their own capabilities.”
More advanced Maximo modules can use augmented reality (AR) to connect local technicians to assistance from the machine’s OEM, enabling two-way video communication. The remote OEM tech can highlight features of the machine and walk the on-site personnel through the repair, eliminating the long wait that sometimes comes with OEM maintenance requests. Additionally, the AI system can learn from this as well, enabling it to further improve its ability to assist in machine maintenance.
Like many advances in manufacturing, machine monitoring is a kind of automation in that it automates the gathering and structuring of data. In the case of Maximo, it is using automation to enable manufacturing personnel to improve and learn. “The machine asset of the future will identify failures before they occur,” Dr. Biller says. “The technician of the future will use automation to improve their own capabilities.”
Implementing Machine Monitoring for Machine Shops
According to Dr. Biller, Maximo can often function with the sensors that are already present in most CNC machine tools. If a machine has sensors tracking current, vibration, uptime and downtime, the system should be able to monitor and analyze machine performance. Because the AI can determine what states will precipitate a machine failure on its own, it can often use whatever data is available to accomplish this task. Dr. Biller further recommends starting with the basic Maximo software when first implementing the system. This gives a shop the chance to adjust to the new program before implementing more features. However, the real challenge when implementing Maximo comes before investing in the system.
Dr. Biller says when implementing it in an industrial setting, “The number one cause of failure is a failure to shift the culture.” He suggests that before looking into digital manufacturing strategies, a shop owner should look at how best to change practices. He believes when owners only have fuzzy ideas of how they want to use data, it is difficult to get the shopfloor personnel to buy into the process. If the personnel are unwilling to work with the owner, the AI system will have a harder time learning how to best serve the facility, and the personnel will not benefit from its capabilities. “It takes a cultural transformation from within the facility,” Dr. Biller says. “But once the manager gets the floor personnel to buy into the process, the efforts pay off.”