Change can be overwhelming, whether in life or business. But in today’s machine shop, the real risk lies in resisting change. While some shop owners fear making changes due to the short-term disruptions that may occur, failing to evolve can cause a business to fall behind competitors and even jeopardize long-term success.
Our industry is constantly changing – are you keeping up? Let’s explore how you can make change a part of your business plan.
Why Change Is Essential in Today’s Machine Shop?
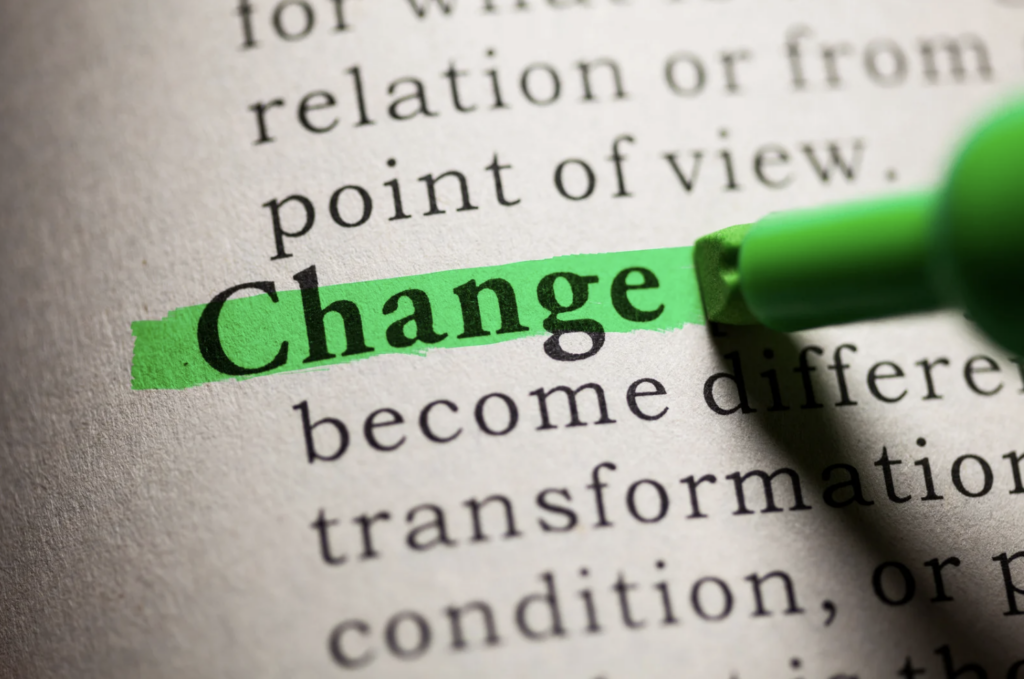
External pressures are constantly evolving
The economic and regulatory landscape is shifting rapidly, affecting everything from machining safety requirements to supply chain logistics. Government policies, tariffs, and market demands can transform the industry overnight. Shops that resist change may find that they’re struggling to adapt when external forces make adjustments imperative.
Competition demands innovation
What worked yesterday, and even what works today, may not be optimal tomorrow. A shop that once had the best pricing and turnaround times in the state 10 years ago could now find itself outpaced by competitors who are faster to adopt new technologies and processes.
If your competitors are investing in manufacturing efficiency and producing parts in a fraction of the time, it’s essential that you follow suit or risk being left in the dust.
Don’t Wait to Change: 7 Ways to Improve Manufacturing Productivity and Efficiency
1. Invest in technology and workforce training
One of the most effective ways to ensure your shop stays ahead is to invest in automation, upgraded machinery, and training programs. Whether through established training centers or in-house development, keeping your workforce up to date on the latest machining techniques helps you stay competitive.
2. Embrace change as a business strategy
Shops should not view change as a last resort but as an ongoing strategy. Instead of making changes only when things go wrong, plan for continual enhancements in processes, equipment, and workforce development.
3. Seek out employee buy-in
It’s common for change to be met with resistance, particularly from employees who are comfortable with the status quo. However, when employees feel informed and actively involved in the process, adopting new systems and practices becomes far smoother. Here’s what you should do to encourage buy-in:
- Engage teams early in the process rather than surprising them with last-minute announcements.
- Explain the benefits of any and all changes. When employees understand the impact these changes could have on the organization, the odds are better that they’ll get on board.
- Provide training to ease any transitions. It’s your responsibility as a business leader to ensure your people are comfortable navigating brand-new equipment or processes. When your team feels confident, adoption will come more naturally.
4. Optimize your machine shop organization
A well-structured shop floor improves workflow, reduces downtime, and enhances safety. Strategically consider your specific operations, particularly where you shine and where bottlenecks may exist within your facilities. We suggest evaluating how lean manufacturing principles and digital technologies can help streamline processes and increase production.
5. Leverage manufacturing networks and resources
If you’re unsure about the best steps forward, turn to industry peers for insights. Our online forum, NTMA Connect, provides valuable opportunities for collaboration and learning. No need to wait for your next chapter or national event to start picking other members’ brains – simply interact on NTMA Connect for immediate access to your manufacturing network.
6. Re-evaluate your suppliers
Optimizing costs often starts with your supply chain, and you should periodically reassess supplier agreements to ensure you’re getting the best value. NTMA’s exclusive cutting tool program with PTSolutions can help shops reduce costs while continuing to source the high-quality tooling they need.
7. Stay up-to-date on industry updates
Today’s machine shops should stay in the know about major developments in the manufacturing sector. New regulations and policies can have a variety of impacts on your operations, so it’s essential to stay informed and remain ready to pivot as needed. NTMA’s manufacturing advocacy efforts help members navigate local, state, and federal policy changes and adjust their business strategies accordingly.
Change Is an Opportunity, Not a Threat
Change isn’t the enemy; rather, not moving forward is the real risk in today’s machine shop. Change can feel uncomfortable, but it’s necessary for growth, efficiency, and longevity. Whether it’s through improving manufacturing processes, adopting new technology, or restructuring your machine shop business plan, embracing change as a constant is the key to ensuring long-term success.
Want to learn more? Leverage your NTMA membership!