This article by Julia Hider originally appeared in Modern Machine Shop magazine.
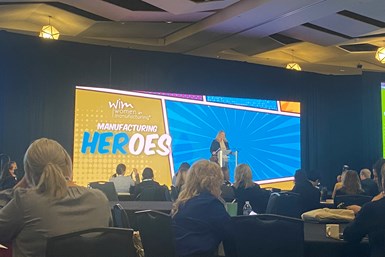
Between the coronavirus pandemic, racial justice protests, supply chain disruptions and worker shortages, 2020 and 2021 have been difficult years. The 2021 Women in Manufacturing Summit, with its theme of “Manufacturing HERoes,” not only celebrated challenges overcome, but also focused on how manufacturers could address current pain points.
Whether in the context of a supply chain or a workforce, the value of building diversity was a common theme of the discussions and sessions. Building diversity can be a challenge, just like any change, but the effort is worthwhile because diversity is a strength that can help solve some of the difficulties the manufacturing industry continues to face.
Supply Chain
According to recent data from the U.S. Census Bureau’s Small Business Pulse Survey, 64.6% of small manufacturers have experienced domestic supply chain disruptions. Vanessa Miller, a partner at Foley & Lardner LLP who focuses on supply chain disputes, says manufacturers who focus on diversification can make their supply chains assets, not liabilities.
In a presentation titled, “Supply Chain: Lessons Learned the Hard Way Navigating COVID-19 and Other Obstacles,” she cited supply chain mapping as one way to diversify. It’s typical for companies to know where their suppliers are, but it’s important to figure out where all of the sub-suppliers are, down to raw materials, to ensure that supply chains are truly diversified. This is why transparency is so important, according to Miller. She also notes that, while diversifying a supply chain has costs, there are dangers in having only one supplier, especially if that one supplier is the cheapest option. “There needs to be some kind of balance there,” she says. At the very least, manufacturers should identify backup suppliers and work with customers on pre-qualifying them or setting up an expedited approval process.
These strategies will be important in the long term because Miller predicts continuing supply chain difficulties. “This is not just a COVID issue,” she says. “It’s really ongoing.” In addition to the pandemic, problems also stem from the globalization of supply chains; the electrification of more products (requiring more chips and batteries); use of just-in-time workflows; labor shortages; and instability in the freight market.
Hiring
Another presentation from Kathy Steele, CEO of growth consultancy firm Red Caffeine, focused on how embracing diversity can also help with a longer-term problem: the skills gap.
Unlike the present supply chain issues, the skills gap is not a new problem. Manufacturers have been feeling the effects of a shortage of skilled workers for years. According to research from Deloitte and the Manufacturing Institute’s 2021 Manufacturing Talent Study, the U.S. manufacturing industry is expected to have 2.1 million unfilled jobs by 2030. And with labor shortages now affecting many industries, the situation remains difficult. Data from the same study showed that U.S. manufacturing executives believe that finding the right talent is now 36% harder than it was in 2018.
Given these realities, “Our hiring strategies need to fit the way people want to work today,” Steele said. This could include hiring consultants or gig workers instead of traditional full-time employees. She also encouraged companies to find new sources for talent, citing the Mom Project, which helps women remain active in the workforce, as an example. While new groups of employees may need different accommodations, such as flexible schedules, these are trends that are already happening in the workforce in general, and Steele encourages companies to embrace these trends if they can. “Either we start to think like this, or we won’t be able to grow our businesses,” she says.
Steele also encourages companies to think strategically about where to recruit new hires instead of going after the same group of people. Companies should then build recruiting strategies around these candidates by going to where they are. For example, a lot of manufacturing jobs don’t require employees to be at a computer all day, so having a hiring platform that can communicate with candidates via text is helpful. Or maybe employers offer a flexible schedule for caregivers or tuition reimbursement for employees who want to further their education, so they need to think about where they can go to recruit people who will be drawn to these benefits. “This isn’t just about diversity and inclusion,” she explains. “It’s about thinking differently about staffing.”
Whatever “thinking differently” entails, the time and effort are likely to be worthwhile because leaving positions open costs money beyond lost capacity. It’s obvious that having an unfilled job isn’t good for a company, but according to Steele, for a job that pays $50,000 per year, the company loses $450 in revenue every day that job remains open. So while companies have to spend money to recruit new employees, the cost of leaving the job open is also significant. She notes that, while companies typically spend 70% of their budgets on their employees, they don’t invest proportionally in recruiting these employees.
Retention
Once a company has recruited and trained a diverse workforce, it must work to keep these employees. This means fostering a culture and environment where everyone feels safe and included. Deloitte and the Manufacturing Institute’s 2021 Manufacturing Talent Study also shows that 49% of female manufacturing professionals, 59% of Asian manufacturing professionals and 70% of Black manufacturing professionals surveyed said that their companies should do more to create a diverse, equitable and inclusive environment.
Michele Kaiser, a business unit manager at John Deere Engine Works, traced her personal efforts with diversity, equity and inclusion (DEI) at her plant in a session titled, “DEI – Make It Happen in Your Workplace.” She described how one employee, during a voluntary discussion session, said that although she loved her job and was good at it, she was considering roles elsewhere because she didn’t feel included in the community.
In order to ensure that everyone feels included, Kaiser says that we shouldn’t avoid talking about topics like race in the workplace. She took a number of steps to normalize these subjects within her plant, including a “coffee talk” video series where upper management discussed media and experiences that have shaped their worldviews. These videos, combined with the voluntary discussion sessions during lunch breaks, were successful in engaging employees, which was especially important in an environment where COVID had made connection in the workplace difficult.
Kaiser notes that the goal isn’t to make everyone agree with her perspectives. She adds that when her efforts did bring up disagreements, everyone remained respectful of one another, which counts as a win.