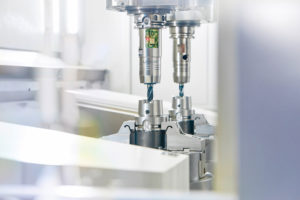
This article by Julia Hider originally appeared in Modern Machine Shop magazine.
Typically, the term “machine monitoring” refers to data that comes from a machine tool, either directly from the control or from a sensor located somewhere in or on the machine. But extending the concept of machine monitoring to other aspects of the machining process can provide more detailed data and allow users to home in on specific improvements.
For those wanting to increase cutting tool performance, the toolholder presents the best opportunity for gathering data. According to Schunk Tooling Group Manager Matt Panosh, the toolholder is the closest non-wearable part to the workpiece, and placing a sensor here can provide valuable information about the cutting tool. (The only closer part to the workpiece would be the cutting tool itself, which is an impractical location for sensors because of wear.) Having a sensor closer to the cut can provide more accurate vibration data than sensors elsewhere in the machine. For example, while sensors in the headstock spindle center might pick up some vibrations, they won’t be able to pick up all of the vibrations caused by the cutting tool, or they could pick up vibrations that aren’t caused by cutting action. “Being closer to the tools offers a much more sensitive system that’s closer to the cause,” he explains.
For this reason, Schunk has developed a smart toolholder, the iTendo, which integrates an acceleration sensor into the center of a Tendo hydraulic expansion toolholder’s axis of rotation to detect vibrations in the metalcutting process. The product of a collaboration between Schunk, the University of Vienna and a software company, the smart toolholder has a 10-hour battery life, and can be charged in a cradle in the toolchanger, or it can be removed from the machine for charging.
In Panosh’s view, a sensory toolholder won’t replace other forms of machine monitoring. But it can complement data pulled from other sources, forming a more complete picture of the machining process.
Using the Data
Once the iTendo gathers the vibration data, it can be used in a number of ways. In the simplest integration, users can collect and save the information. The data can then be transferred to an app on a computer or mobile device, which transforms the raw vibration data into a form that makes separate vibration frequencies and their intensities visible on a graph. The actual mathematical operation involved is inverse Fourier transform (IFT). From here, users can set upper and lower limits for vibration and compare them to the actual IFT output. Schunk is also working on solutions for comparing and exporting IFT data to other software programs, including an Open Platform Communications (OPC) Unified Architecture (UA) interface to transfer the data via Ethernet to other systems in real-time, as well as other algorithms for evaluation.
In addition, the company is developing technology that will enable the toolholder to send out alarms when vibrations go outside the set limits, flagging issues such as broken cutting tools and bad surfaces. The goal is for the toolholder eventually to interact with the machine tool in a closed-loop, self-adjusting system. When the vibration exceeds the determined limit, the CNC would be able to respond to the toolholder signal by adjusting the machine’s spindle override until the cutting tool is stable.
Extending Tool Life, Improving Surface Finish
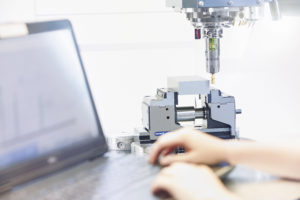
IFT data can give users valuable insight into tool wear and help them extend tool life. “Whether or not an endmill is worn is still a little bit of a mystery,” Panosh notes. Because tool wear can be difficult to see, shops must use other data, such as the number of parts run, as a proxy. But accurate vibration data can give users a much clearer picture. “You’ll be able to get a little bit closer on the wear of the cutting tool and avoid situations where you’re going over the edge, breaking the tool and compromising parts,” he says. He gives the example of a drill that breaks while machining a very small hole. What is happening in the hole is obviously impossible to see, but the vibration monitoring can show evidence, through the resulting data and graphs, suggesting the cause of the break.
“You’ll be able to get a little bit closer on the wear of the cutting tool and avoid situations where you’re going over the edge, breaking the tool and compromising parts.”
The toolholder can also help shops improve surface finishes. Because vibrations and chatter have a negative impact on surface finish, IFT data can give users valuable insight toward achieving good surface finish more reliably.
Applications
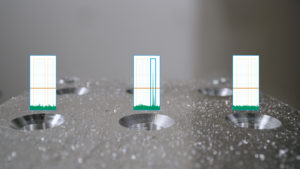
Panosh says the toolholder is compatible with a number of machining processes, including milling, drilling, polishing and grinding. Internal testing has showed that the iTendo can detect tool wear and optimize surface quality of a chamfer for an M20 thread. Schunk is also looking into other machining processes as well, including an application with a brush responding to brush wear. Brushes can be challenging to use in an unattended process because of the difficulty monitoring wear, leading users to throw brushes out even though they still have life left in them. The iTendo could help users get more use out of these and other expensive tools.
While the toolholder wasn’t developed for a specific application or industry, it could be especially useful for applications with long projection tools and thin-walled components, because the vibrations show up especially well in these situations, according to Panosh. It also holds promise for industries that collect and archive manufacturing data, such as medical and aerospace.
Because the vibration limits are set manually, smaller lot sizes would be a challenge for this application of the toolholders. However, future versions will have real-time processing, making smaller batches more practical.
Machine Compatibility
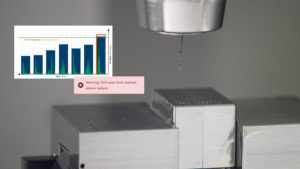
The most basic version of the iTendo, in which the toolholder is used to record data, doesn’t require any integration with the machine tool. More advanced versions, such as the self-adjusting system, will require the support of the machine tool manufacturer and a service technician to integrate. The company’s headquarters in Germany is working on an integration with Siemens controls, and other brands will follow. These integration will require newer machine tools with digital and analog inputs and outputs and the ability to address them in the NC program, as well as the ability to exchange information via OPC UA.
The toolholder itself is compatible with HSK-A63 20 mm diameter × 130 mm projection length spindle interfaces. The company is working on offering other interfaces, such as CAT40. The size of the electronics prevents the use of shorter holders, but the company is working on modifications for that as well.
Schunk has rolled out the data collecting version of the toolholder for testing in Europe, and Panosh expects to have demo kits to show in the U.S. this year, with more advanced versions of the toolholder to follow.